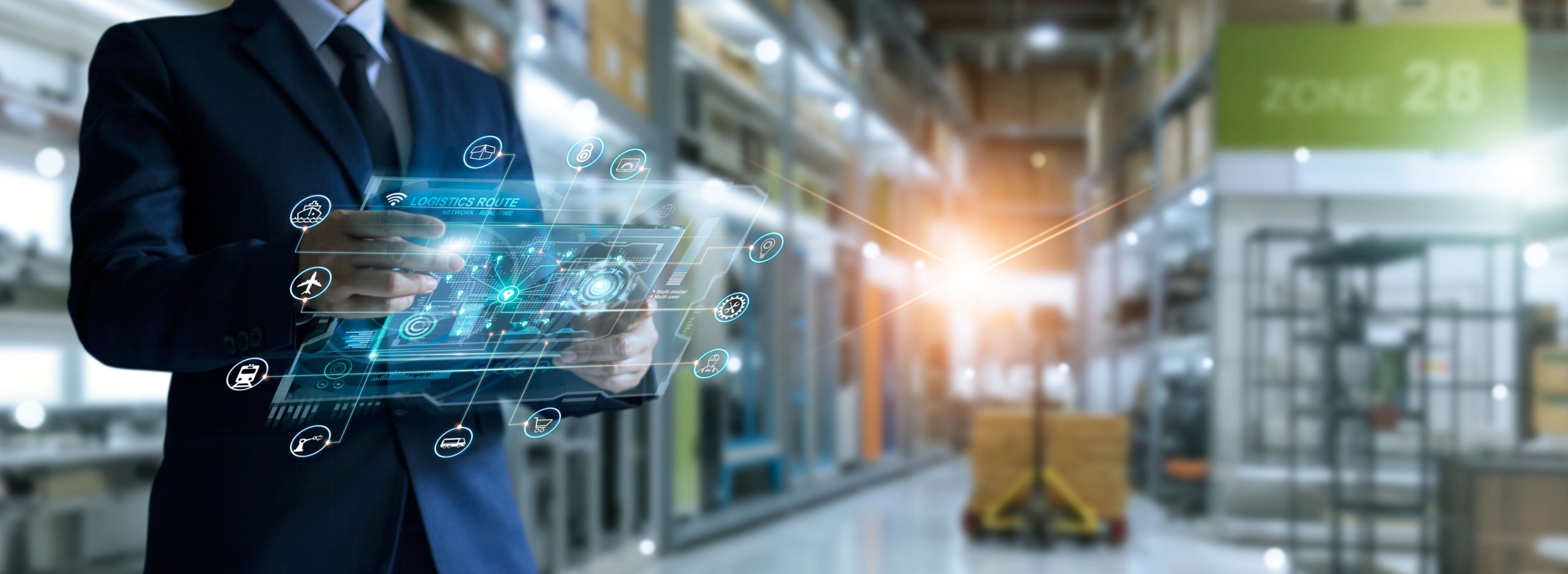
What does the crystal ball reveal about this year’s developments in the warehousing industry? Our experts at DJ Products, makers of the electric Trailer Dolly, share some insights about the top five warehousing trends taking shape in 2023.
1. Automation
Automation of warehouse processes improves workplace safety while also reducing the possibility of human error.
-
- Amazon and UPS are two of the companies that have begun to incorporate drones in their delivery services. Ware, supplier of automated inventory systems, offers autonomous drones that fly inside warehouses, using 2D scanners and stored location data to map a digital “twin” of the facility.
-
- Peer Robotics has developed mobile robots with sensing technologies to collaborate with human workers.
2. Wearables
Digital wearables enable workers to utilize high-tech tools without the need to carry them around.
-
- Ox, a US-based startup, has smart glasses fitted with scanners and real-time messaging systems to maximize pick routing and communication between workers.
3. Internet of Things (IoT)
Much like it does in your home, the Internet of Things uses technology to automate and simplify functions such as climate control and lighting.
-
- Track inventory and personnel with an IoT beacon from ScratchNest, which sends signals to smart phones and tablets via Bluetooth. The beacon also has extended battery life for better performance.
4. Sustainability
Companies continue to search for ways to minimize their carbon footprint and reduce their impact on the environment.
-
- Leave petroleum-based pallet wraps behind with innovative solutions from Australia’s Great Wraps. Their innovative wraps are made from converted food waste, which decomposes into carbon and water for toxic-free disposal.
5. Fleet Management
Forklifts are involved in a high number of warehouse accidents, causing significant injuries and damage. Telematics solutions allow for safe and effective interaction between workers and equipment.
-
- Onyx, a telematics system from GemOne, collects data on its proprietary hardware system and stores information on a cloud platform for easy retrieval.
Improve Productivity and Safety with the Trailer Dolly
Our battery-powered tugs, movers and pushers are eco-friendly solutions for your material handling needs. Contact us at 800.686.2651 or use our convenient online chat feature to learn more from our friendly and helpful Sales Engineers.