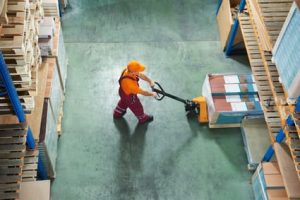
Quality material handling equipment improves productivity, but those gains can be offset by inventory loss, eating away at profits. Between damages, poor inventory control and theft, losses that seem insignificant on a daily basis can add up to considerable amounts.
While some loss is unavoidable, you can take steps to limit inventory shrinkage. Incorporate these tips in warehouse day-to-day operations to reduce inventory loss and protect profits.
Reduce Risk of Damages
Inventory damage occurs primarily due to packaging or handling. Review incidents of damage over time to see if you can discover a pattern.
– Make sure packaging materials are sturdy enough to accommodate products and stand up to specific warehouse conditions, such as extreme heat or cold.
– Limit the amount of headspace in packages to prevent boxes becoming crushed, especially when they’re stacked on a shelf or pallet.
– Train employees in proper loading techniques.
Improve Inventory Control
High-tech warehouse management systems (WMS) allow for greater precision when tracking inventory. Traditional methods such as inventory auditing and cycle counting programs also minimize the risk of lost products.
Increase Security Measures
No one wants to think about in-house theft, but it’s an unfortunate fact of life. Strategically placed video cameras can serve as deterrents while providing a means of investigating instances of pilferage. If your warehouse stocks products with a high value on secondary markets, consider instituting a consistent and fair inspection program in which all bags are searched.
Upgrade Warehouse Safety with Material Handling Equipment from DJ Products
Are workers struggling with heavy loads? Our battery-powered material handling equipment reduces risk of both inventory damage and workplace injury. Visit our website and let our knowledgeable sales engineers help you find the perfect tug, pusher or mover for your application.