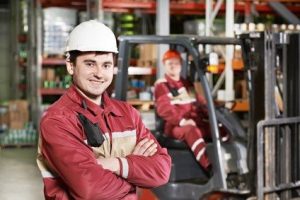
Does it feel like the air in your workspace is so heavy lately that even the strongest material handling equipment couldn’t lift it back up? If laughter in your workspace is but a vague memory, your employee morale needs a boost!
Low Morale = A Losing Business Scenario
Employee morale can make or break a company’s success. Low morale zaps productivity, amplifies grouchiness and lack of cooperation, and increases turnover. Keeping an eye on morale and strengthening it when times are tough are integral to helping your business achieve its goals.
Creative & Easy Ways to Strengthen Morale:
1. Help Employees Understand Their Work Serves a Higher Purpose.
It’s easy for employees to lose their sense of purpose in the daily grind. However simple postings of ‘I Got a Job’ stories from recently hired, grateful job seekers who snagged a spot with the company can help highlight the value of job positions.
2. Celebrate Accomplishments.
In your quest to get ahead, don’t forget to look behind, recognizing significant accomplishments of team members annually.
3. Give Employees the Chance to Recharge.
With adequate time off that grants an energizing break from regular responsibilities, whether in the PTO or creative office party arena. S’mores Friday, anyone?
4. Mix-It-Up.
Doing the same thing day-in-day-out is boring. Shake things up with office Olympics, ping-pong tournaments, or simple impromptu cookout lunches.
5. Have Fun.
Conduct a monthly lotto for participation in a card, board game, or Wii bowling match. Or reward workers with gift cards for play-days at amusement parks or other fun area events.
Boost morale by showing you care with ergonomic material handling equipment designed to prevent injuries, make work easier and more efficient, and reduce labor. Learn more from DJ Products today.