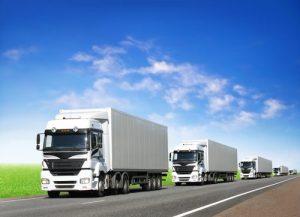
With Amazon, Target, and the like offering increasingly faster shipping times at little to no additional cost to entice customers, the pressure is on. Those moving goods from the docks via terminal tractors, toting it via tractor trailer, and delivering door-side are all under a time crunch. As the ‘need for speed’ becomes increasingly pressing, how can your business keep up the pace?
Five Supply Chain Logistics Tips for Meeting ‘Instant Gratification’ Needs:
1. Get Closer
Instead of one large distribution center, consider a number of smaller centers to place yourself closer to customers/shippers and speed the flow.
2. Invest in the Right Equipment
Instead of constantly waiting on hostlers, invest in terminal tractors that can be driven by any employee – no CDL or Health Card required. Not only do these motorized trailer dollies offer faster movement, but they improve safety and control, reducing the risk of injury and damage.
3. Make Friends
If you’re a smaller firm, increase your shipping range with the help of a partner, such as local couriers or ShipBob. This nationwide service holds goods in its warehouses, picking, packing and shipping them for small-to-medium sized companies to nearby consumers, shrinking shipping times.
4. Embrace Tech
This includes a number of recent innovations, including:
– Data analytics for better planning.
– Visibility tools that allow you to quickly identify what/where your inventory is.
– Internet of Things (IoT) tools that enable better inventory tracking, segmentation, and placement.
– Predictive analytics to uncover disruptions before they occur.
5. Automate
Sorters, conveyors, and robots are a great way to speed up a range of distribution and fulfillment processes, as are autonomous vehicles.
Running behind? Get your supply chain running a little faster with the help of terminal tractors from DJ Products today.