All the major economic shifts and advances in technology are impacting the transportation and logistics industry. Everyone hears about eCommerce, the blockchain, augmented reality – but in logistics, these buzzwords are already impacting our bottom lines. Let’s dive into the logistics trends for 2019 to anticipate and stay ahead of the game.
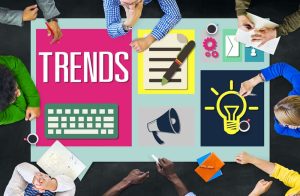
Machine-driven processes may have the most direct and immediate impact. From robotic picking to new semi trailer movers that tow freight around the yard, any warehouse can benefit from upgrading its material handling equipment.
Accounting and consulting firm PwC recently released Transport and Logistics Trends 2019.
Logistics and the Economy, 2019
First, let’s consider some of the market forces at play:
– Mergers and acquisitions: 38 percent of CEOs are planning an M&A event in the next year. Would consolidation improve your efficiency? Is a competitor about to get much larger?
– International trade deals and trade wars: Are you ready to pivot when the next political move results in shifting trade routes and priorities?
– Rail traffic and trucking shortages: Logistics firms expect the pressure on freight transport to continue. Can you improve warehouse efficiency to mitigate high delivery costs?
All this drama takes place against a backdrop of a strong economy and optimistic forecasts. Money is being made, and the stakes are high. Smaller firms need to stay agile and invest in improvements to come out on top rather than getting eaten up by the behemoths.
The Next Big Thing in Logistics
In Part Two, we’ll look at software and technology trends in logistics. From augmented reality warehouses to automated material handling and semi trailer movers, 2019 will see plenty of changes on the ground and in the cloud. Contact us at DJ Products for more info about trailer movers.