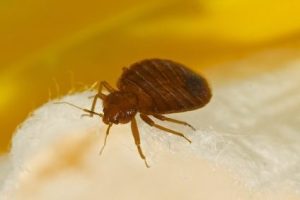
Over the Past few years, reports of bed bugs in hotels have received a great deal of media attention. Despite this fact, the hospitality industry is fighting an even greater battle with the public’s lack of general understanding regarding bed bugs.
Battling Public Misinformation
Researchers at the University of Kentucky recently conducted a survey to explore public perception of bed bugs in hotels. While 60 percent of respondents said they would move to a different hotel if they discovered evidence of bed bugs, no more than 25 percent would do the same with problems like smoky rooms or dirty linens.
Surprisingly, most respondents don’t know what bed bugs look like. When shown a “lineup” of five different insect pests, only 35 percent of business travelers and 28 percent of leisure travelers recognized the bed bug.
More than half the respondents said they would avoid a hotel that had a single online report of bed bugs. Jerrod M. Penn, PhD, lead author of the study, expressed concern at this finding, citing the unreliability of online reviews.
How Should Hotels Respond?
Wuyang Hu, PhD, senior author of the study, suggested a two-pronged approach to the issue:
- Train hotel staffs to recognize bed bugs in the early stages.
- Develop a reputation management plan to respond to online reviews as well as incidents within the hotel.
Improve Employee Safety and Job Satisfaction with Hotel Equipment Movers from DJ Products
Make sure your staff has the right tools to perform their jobs safely and efficiently. Visit our website to learn more about our electric hotel equipment pullers and movers such as our best-selling CartCaddyLite.