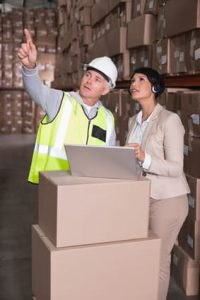
The shift toward dimensional weight shipping rates has triggered a cascade of changes on warehouse management. Many warehouses are sidestepping the higher rates by using polybags or Tyvek mailers instead of boxes.
Along with the potential savings, soft bags present a new set of challenges compared to the familiar and reliable process of handling rectangular boxes.
As Alexander Communications points out, polybags require new technology for picking and scanning. The ultimate cost savings, however, should drive warehouse managers to analyze whether products can be mailed in polybags and how to make the process effective.
Key considerations for using packaging solutions to circumvent dimensional weight shipping charges:
- Scanning and sorting solutions must be able to handle irregular shapes.
- Material handling can become more efficient because more items can fit in a cart and be transported with motorized warehouse tugs.
- Warehouses can often find ways to ship some, if not all, products in bags. Using both bags and boxes does not necessarily present an insurmountable challenge.
- Customers can be charged dynamic rates based on actual shipping — or flat rates that protect your margins when boxes must be used.
Be sure to not overlook the changes that polybag shipping will have on material handling inside the warehouse. Instead of a pallet with several large boxes, you may have a cart weighted down with many more products in polybags. Warehouse tugs automate this movement to streamline the process and protect workers from injuries.
When cost savings are on the line, the boost in productivity from warehouse tugs can maximize the benefits of new packaging solutions. Visit DJProducts.com for more info about industrial cart movers.