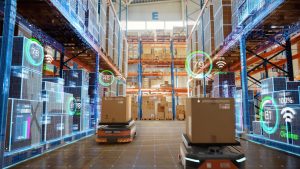
Warehouses and distribution centers are heading into 2023 with many opportunities and challenges. Safety improvements are always important, making the use of trailer dolly solutions an ongoing trend. From supply chain and inventory solutions to increased interest in the use of automation, these are some of the other top trends in the warehouse and distribution industry for the new year.
Electric Delivery Vehicles
More companies are looking into using electric delivery vehicles to help cut down on pollution, noise, and costs. This involves the use of smaller vehicles, such as vans and small trucks, rather than box trucks. The use of these smaller vehicles is more practical in some areas, while also offering a way to reduce environmental damage.
Autonomous Lift and Reach Trucks
The use of forklifts in warehouses and distribution centers comes with a risk of injuries. Businesses are exploring the possibility of using autonomous lift and reach trucks to improve safety and efficiency. These trucks can make it easier to move items around with a lower risk of worker injuries.
Neighborhood Distribution Centers
Real estate costs and limited inventory on the market are pushing business owners to find other solutions for storing products. Some are turning to neighborhood distribution centers or mini-warehouses for storing goods. These localized distribution centers and warehouses could help make up for a lack of larger warehouse space.
Automation
With the rise in eCommerce, warehouse and distribution center owners are showing a growing interest in adopting automation. The use of automation can offer a solution to the problems the industry faces due to supply chain issues, labor shortages, and rising costs.
Supply and Inventory Solutions
With the supply chain improving in some areas, companies are looking into solutions for managing inventory more efficiently. Some companies face shortages of certain products, while others are dealing with too much inventory. Solutions might involve reducing prices on overstocked items or finding ways to obtain low inventory items.
If you’re looking into solutions for moving large vehicles safely in warehouses, hangars, or other facilities, please contact DJ Products. We offer trailer dolly solutions that make it much safer to pull or push large vehicles and other items.