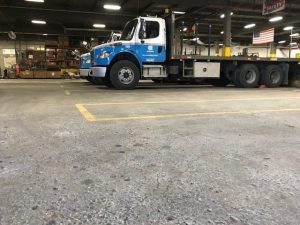
In the trucking industry, success leans heavily on logistics. Detailed coordination needs all parts involved running smoothly to function efficiently. From the necessary acquisition of durable, heavy-duty vehicles to the utilization of useful trailer helpers, like a semi trailer dolly, every working piece needs to fit correctly to sustain a well-oiled profit-making machine.
Lately, the need for immediate product acquisition and delivery services has been steadily climbing. A recent article describes a disturbing trend that reveals the trucking industry is at a crucial time in its history – a veritable tipping point! High demand is creating real concerns for those in trucking and logistics as employers scramble to meet the needs of their customers.
Unwrapping the Rear Axle
Trucking business owners are keeping their used trucks close to the vest rather than trading them in for newer models. And they are purchasing newer models as well. The need is growing for reliable new and used semis so tractor/semi-trailer manufacturers are racing to keep up. It’s vital to businesses inherently dependent on their ability to deliver freight quickly to ensure there is no slow down in the logistics process.
Logistics emphasizes the need to acquire and retain reliable machinery to help deliver products on time and with care. Get rid of the confusion, safety concerns, labor costs and increase your potential to deliver freights. Quality inventions like a semi trailer dolly can take up the slack when a portion of the process falters.
DJ Products Keeps Freight Moving
Premium quality machinery solves difficult issues with ingenuity. When demands are high and supplies are low, the right products allow you to meet higher levels of expectations. DJ Products continues to reach across a multitude of industries to provide tested solutions to complex problems.